Sika Deutschland
Nuovo concetto di intralogistica per processi più snelli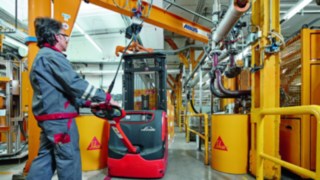
Processi di flusso di materiale precisi per un parco di carrelli elevatori e attrezzature da magazzino perfettamente uniforme: Sika Deutschland GmbH, la società affiliata del complesso multinazionale svizzero e uno dei maggiori fornitori mondiali di sistemi di prodotti chimici per l’edilizia e adesivi e sigillanti industriali, raggiunge questo obiettivo con un concetto logistico completo che, nonostante presenti soluzioni su misura, punta sull’uniformità, si affida a un unico marchio di carrelli elevatori e usufruisce del leasing full-service.
Sika Deutschland appartiene a quelle aziende per cui una gestione aziendale efficiente e sostenibile è prioritaria. Allo stesso modo, l’ottimizzazione della logistica interaziendale è fortemente radicata nella filosofia aziendale. La sede produttiva di Bad Urach, ai piedi delle Alpi sveve, ne è un esempio. Qui le materie prime, per lo più naturali, vengono fornite in enormi contenitori o fusti e, a causa del loro elevato ingombro, vengono processati il più velocemente possibile. “Il materiale proveniente dalla produzione viene direttamente trasportato presso il magazzino centrale a Stoccarda, nel distretto cittadino di Weilimdorf e lì preparato per gli ordini,” come afferma Michael Rath, Direttore dello stabilimento di Bad Urach. La sede di Bad Urach non dispone di un magazzino in cui stoccare il prodotto finito. Una media di sette autocarri al giorno raggiungono le rampe di carico, mentre altri veicoli vengono caricati nel cortile.
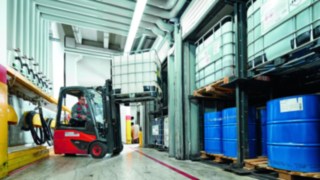
Carrelli elevatori elettrici Linde al lavoro presso Sika Deutschland GmbH
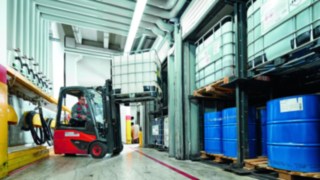
Carrelli elevatori elettrici Linde al lavoro presso Sika Deutschland GmbH
I responsabili della logistica dello stabilimento di Bad Urach si trovano spesso a dover affrontare le difficoltà legate alla mancanza di spazio. Dei passaggi stretti e degli spazi angusti per le manovre sono il loro pane quotidiano. Altri fattori includono le capacità di carico del soffitto limitate, nonché il soffitto basso e l’altezza di passaggio ridotta. La produzione all’interno di questo edificio storico del 19° secolo è suddivise in due aree: da un lato gli adesivi e i sigillanti mono- e bicomponente per diversi impieghi industriali, come elementi di rotaie, turbine eoliche, sigillatura di finestre o container refrigerati, mentre nell’altra area vengono realizzati resine ad alte prestazioni, pannelli e paste per la costruzione di modelli e stampi di automobili, yacht o aerei. Un’altra peculiarità della sede di Bar Urach è la sua posizione al centro di questo luogo di cura rinomato per l’aria salubre. “Poiché siamo vicini al centro della città, abbiamo deciso di rinunciare completamente ai carrelli elevatori a combustione,” afferma Michael Rath. “Soddisfiamo le elevate esigenze ambientali con processi sicuri e un monitoraggio continuo.”
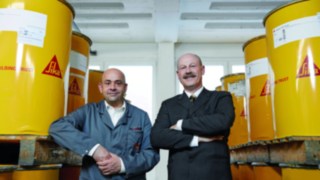
Michael Rath, Direttore dello stabilimento di Bad Urach e Atilla Böhm, Direttore del parco vetture
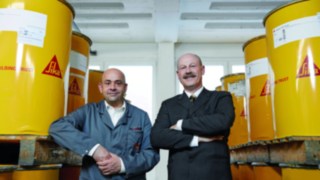
Michael Rath, Direttore dello stabilimento di Bad Urach e Atilla Böhm, Direttore del parco vetture
“Per soddisfare il nostro fabbisogno elettrico sfruttiamo già oggi l’energia idraulica prodotta dal fiume che attraversa i nostri stabilimenti. In futuro desideriamo portare la quota ricavata da questa fonte a circa il 40-45 %,” spiega il Direttore dello stabilimento. L’ampio assortimento di prodotti rappresenta anch’esso una sfida. “Dobbiamo reagire a questo aspetto e alle fluttuazioni delle quantità di produzione con una giusta flessibilità nei nostri processi,” sottolinea Michael Rath. Inoltre, alcune aree di produzione sono classificate come aree con rischio di atmosfere esplosive zone 1 e zone 21. In queste aree, sussiste il pericolo che miscele di aria e gas combustibili, vapori o nebbie o polveri combustibili presenti nell’aria si formino occasionalmente nel corso del normale funzionamento. I carrelli industriali che vengono impiegati in queste zone necessitano, quindi, di un certificato di esame CE per tutti i componenti rilevanti per la sicurezza.
Nuova strategia d’acquisto
All’incirca quattro anni fa, l’azienda, con sede principale a Stoccarda, ha deciso di elaborare un concetto generale di intralogistica. “Così facendo, volevamo garantire che gli investimenti per i carrelli industriali e il software del parco macchine avessero un impatto maggiore sull’efficienza dei nostri processi di produzione,” spiega riguardo all’obiettivo posto Attila Böhm, Direttore del parco vetture di Sika Deutschland GmbH. In stretta collaborazioni con i direttori dello stabilimento e i responsabili del flusso materiale di tutti e sette gli stabilimenti di produzione tedeschi, al termine della fase concettuale, il Direttore del parco vetture ha definito tre direttive fondamentali su cui basare la nuova strategia d’acquisto. La prima decisione è stata di passare dai veicoli di proprietà a quelli in leasing full-service. Attila Böhm sottolinea:
Un contratto di noleggio stabilisce con chiarezza le responsabilità e consente di avere sempre in uso tecnologia di ultima generazione.
In linea con questa idea vi è anche la seconda direttiva, ovvero, di scegliere un unico marchio di carrelli elevatori, idealmente per tutti i siti. “Per tutte le questioni inerenti ai nostri carrelli industriali, la soluzione ideale è quella di avere un unico interlocutore. In primo luogo, questo ci dà il vantaggio di poter contare sempre sugli stessi tecnici di servizio che, quindi, sanno come muoversi. In secondo luogo, tutti gli apparecchi si basano sullo stesso concetto di commando e non vi è alcuna necessità di adattarsi. Ne risultano maggiore produttività e sicurezza nello stabilimento. In terzo luogo, intendevamo garantirci le migliori condizioni possibili attraverso la conclusione di un contratto quadro,” afferma Attila Böhm. Allo stesso modo ammette che questa strategia non è in linea con la via percorsa da altre aziende, come quelle dell’industria automobilistica. In questi settori si continua a puntare sulla strategia adottata in precedenza anche da Sika Deutschland, per cui si coopera su una base ampia e collabora con diversi produttori di carrelli industriali. “Con piena consapevolezza abbiamo optato per un approccio diverso, così da ottimizzare i nostri processi,” spiega Attila Böhm. La terza regola della nuova strategia d’acquisto verte sulla riduzione della varietà di modelli. “Invece di utilizzare carrelli con capacità di carico diverse, ad esempio, ora utilizziamo solo il modello più grande e siamo flessibili”.
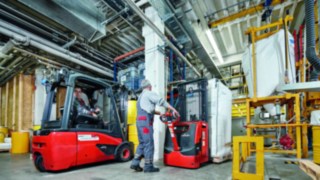
Requisiti elevati in termini di logistica
Secondo quanto afferma il Direttore dello stabilimento, Michael Rath, la decisione di Sika di puntare su Linde Material Handling come fornitore esclusivo è dovuto sia alla rete di servizio capillare dei partner commerciali di Linde, con Schöler Fördertechnik nelle vesti di concessionario principale, sia alla facilità d’uso dei veicoli Linde.
“Per noi è stato chiaro che dovevamo coinvolgere i nostri dipendenti nel processo di selezione. In tal senso, la decisione doveva essere basata su criteri oggettivi e fatti, invece di intuizioni o abitudini. Abbiamo quindi fatto compilare ai nostri carrellisti dei moduli di valutazione e sottoposto i veicoli di diversi costruttori a test di paragone intensivi,” così Michael Rath descrive il processo decisionale.
Il risultato finale è stato univoco: tutti i siti hanno optato a maggioranza per Linde.
Nel frattempo, la flotta è stata gradualmente rinnovata. L’ultimo arrivato è uno stoccatore con protezione contro le esplosioni, a interasse ridotto e dotato di un accessorio speciale per sollevare e ribaltare fusti aperti o chiusi. Non appena avremo ricevuto tra un paio di settimane questo portafusti ribaltabile per l’area di protezione in atmosfera potenzialmente esplosiva, il progetto sarà temporaneamente concluso.
“Nonostante abbiamo adesso sei mezzi in meno, siamo riusciti a ottimizzare molto le nostre procedure di intralogistica,” riassume il Direttore dello stabilimento Michael Rath. Ciò è stato possibile, non da ultimo, grazie alla gamma di attrezzature e optional montabili, ora notevolmente ampliata, e dalle soluzioni su misura. Ben due terzi dei complessivamente 30 carrelli elevatori e attrezzature da magazzino impiegati nell’impianto sono dotati di soluzioni su misure delle condizioni locali.
Per trasportare i numerosi contenitori merce e container sovradimensionati, alcuni carrelli elevatori e transpallet, ad esempio, sono stati dotati di forche particolarmente lunghe. Un’altra innovazione nella pianificazione del flusso di materiali, che è stata posta in essere dal 2013 con la sostituzione del parco carri industriali, è che i fusti, i contenitori e i pallet vengono pesati e trasportati alla rispettiva destinazione nella stessa fase di lavoro.
Il miglioramento continuo dei nostri processi è per noi un aspetto fondamentale.
Michael Rath, Direttore dello stabilimento Sika a Bad Urach
La manutenzione preventiva assume una posizione di rilievo
Il prossimo lancio della soluzione per la gestione delle flotte Linde, “connect:”, rappresenta un’occasione ad alto potenziale. “Le basi di requisiti tecnici di sistema in fabbrica le abbiamo già poste,” spiega il Direttore dello stabilimento Rath. I responsabili dei flussi materiale prevedono un’ulteriore ottimizzazione dei processi e una maggiore sicurezza, in particolare, durante il funzionamento, grazie a funzioni quali il controllo degli accessi, i sensori d’urto e l’analisi dell’utilizzo.
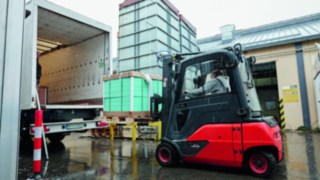
Un carrello elevatore elettrico Linde in fase di caricamento presso lo stabilimento Sika
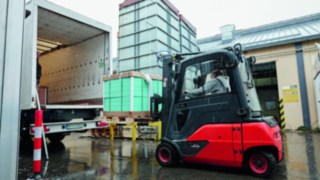
Un carrello elevatore elettrico Linde in fase di caricamento presso lo stabilimento Sika
La trasmissione dati dal carrello elevatore alla rete aziendale avviene tramite il Wi-Fi. “Stiamo pensando di sfruttare questa rete di dati in ottica futura anche per la manutenzione preventiva,” spiega il Direttore del parco vetture Böhm. “Nella prospettiva ideale, il carrello trasmette i messaggi d’errore direttamente al nostro partner di servizio. Quando il tecnico di servizio Schöler raggiunge gli stabilimenti, ha già pronto con sé il pezzo di ricambio adatto”. L’impianto di Bad Urach diventerebbe così nuovamente un sito pilota per una soluzione innovativa nell’ottimizzazione dei processi.
Informazioni su Sika Deutschland GmbH
Da società affiliata del complesso multinazionale Sika AG, Baar in Svizzera, e con più di 1.100 dipendenti e ben 545 milioni di Euro di fatturato annuo, Sika Deutschland GmbH e uno dei maggiori fornitori mondiali di sistemi di prodotti chimici per l’edilizia e adesivi e sigillanti industriali. Sika ha ricevuto nel 2015 il Premier Automotive Suppliers’ Contribution to Excellence (PACE) Award per la colla Sikaflex Ultra-High Modulus, prodotta presso lo stabilimento di Bad Urach. Questa colla a rapido indurimento viene utilizzata, tra l’altro, nella produzione delle BMW i3 e i8 per l’incollaggio del modulo “Life”, l’abitacolo in plastica rinforzata con fibra di carbonio, e del modulo “Drive”, il telaio in alluminio.