Heidelberger Druckmaschinen AG
Una ventata d’aria fresca (di stampa) nella logistica di Heidelberg
In un’epoca in cui i desideri dei clienti sono sempre più personalizzati anche l’intralogistica deve adattarsi gradualmente alle condizioni di produzione modificate. L'esempio di Heidelberger Druckmaschinen AG (Heidelberg) a Wiesloch/Walldorf mostra come ciò possa avvenire in un’impresa che agisce a livello globale. Quest’impresa, insieme a Linde Material Handling e al suo partner Suffel Fördertechnik in qualità di appaltatore generale, ha sviluppato un piano di logistica completamente nuovo che ottimizza l’approvvigionamento del materiale delle linee di montaggio di macchine da stampa offset.
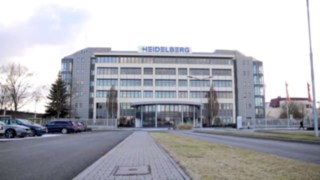
La confezione dai colori vivaci dei corn flakes sul tavolo della colazione, la rivista patinata elegante nella pausa caffè o il biglietto da visita ben rifinito durante il business lunch: anche se il nostro mondo moderno è sempre più digitalizzato, oggi come in passato siamo a contatto ovunque con prodotti di stampa o merce stampata. Anche se diversi gli uni dagli altri, la probabilità che siano stati prodotti su una Speedmaster di Heidelberg è piuttosto elevata. Infatti, questa impresa conosciuta in tutto il mondo con 11.500 collaboratori è tra i leader mondiali del settore. Rinomata nell’ambito della stampa, ha la sua sede principale a Wiesloch/Walldorf, in Baden-Württemberg, al centro della regione economicamente forte del Reno-Neckar, dove si incrociano gli assi della circolazione tra Nord e Sud altamente frequentati di A5 e A6. Qui Heidelberg gestisce la più grande e moderna azienda di macchine da stampa del mondo; su una superficie di un chilometro quadrato vengono prodotte tra l’altro le macchine da stampa offset da foglio leader sul mercato nei formati più disparati.
New challenges –
New Concepts
Heidelberg has been observing a steady change towards greater individuality in the area of customer requirements for a number of years: "Previously, we predominantly built similar printing machines at each site," remembers the Head of Plant Logistics Matthias Ehmler. "Now, we frequently manufacture customized systems and because of this, there has been a sharp rise in the number of different versions," he explains.
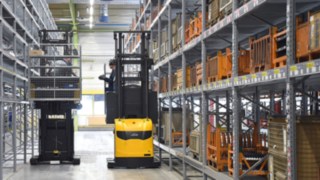
Linde reach trucks and order pickers in the Heidelberger Druckmaschinen warehouse
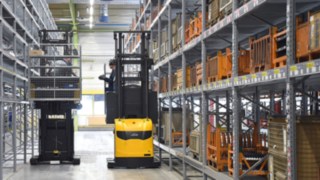
Linde reach trucks and order pickers in the Heidelberger Druckmaschinen warehouse
This customizing trend ultimately also affects the assembly lines: "Workers at the assembly stations were increasingly moving between unmanageable 'material mountains'. The greater the variety, the more parts containers were required. This had an increasingly negative impact on employee productivity," Ehmler explains. "As a result, two years ago, we launched a project to reorganize the assembly department. We wanted to use the production areas more efficiently and bring the material to the worker, not the other way around."
The restructuring of the assembly department towards a modular construction included a reorganization of the intralogistics in the 600-meter-long hall. In future, materials with low daily requirements will no longer be provided in containers on site, rather they will be ordered and picked on kit carts and introduced to the assembly lines by load trains. A central order picking and consolidation area with high racks was set up at the front end of the assembly hall for this purpose. Upstream buffer zones were specified as interfaces for the internal transport systems and as transfer stations for the kit carts.
"Our aim was to ensure a safe, efficient and flexible material supply with the best possible use of the available space," explains the Head of Heidelberger Factory Logistics. An ambitious project, whose implementation during ongoing operation required the perfect meshing of all the different cogs.
Alla ricerca di partner competenti
Con un ampio capitolato di fornitura i responsabili hanno avviato la fase di appalto. «Cercavamo un partner che realizzasse la costruzione degli scaffali e la dotazione di carrelli elevatori compresi di gestione flotta in qualità di appaltatore generale. Al tempo stesso naturalmente doveva essere anche rispettato il piano temporale e dei costi concordato con noi e calcolato in modo fisso, affinché possiamo concentrarci completamente sul management dei dati di base e sulle attività di formazione per i collaboratori», così definisce Ehmler i compiti delle imprese di intralogistica coinvolte. La scelta di affidare la commessa al produttore e fornitore di soluzioni Linde Material Handling insieme al partner Suffel Fördertechnik è stata motivata da più fattori: «Da un lato gli apparecchi Linde hanno potuto ottenere valutazioni positive grazie a elementi di differenziazione, ad esempio per i rimorchi dei carrelli con montanti ad arco del trenino di movimentazione o per il carrello commissionatore ad alto livello di prelievo. Dall’altro lato siamo stati convinti dalla consulenza e infine naturalmente anche dalle condizioni di contratto», conclude Ehmler.
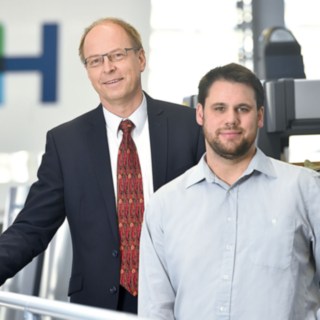
Incaricare lo stesso fornitore della costruzione di scaffali e di carrelli elevatori è stata una scelta positiva per noi, da ogni punto di vista.
Matthias Ehmler, responsabile della logistica di stabilimento
Per consentire l’approntamento dei pezzi sulle linee di montaggio in relazione agli ordini occorreva prima di tutto individuare una soluzione adeguata per il magazzino di picking, cioè per il cuore del nuovo progetto di logistica: «Avevamo già idee e indicazioni concrete nel capitolato. Esse sono state poi elaborate gradualmente con Linde e Suffel dopo la concessione della commessa. Il magazzino di picking doveva consentire lo stoccaggio di pezzi di grandi e piccole dimensioni nonché di intere unità costruttive, permettere diverse geometrie dei contenitori e al tempo stesso rispettare gli elevati standard in termini di tutela del lavoro», così il responsabile di progetto Stefan Heger riepiloga le sfide principali.
Supermercato ben assortito
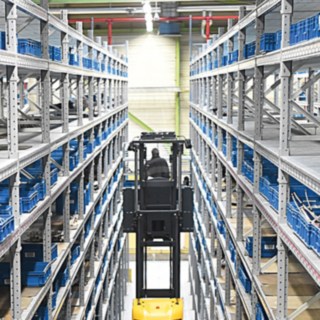
Il nuovo magazzino verticale con 13 file di scaffali e 4.500 codici articoli funziona come un supermercato ed è costituito da un’area con corsia larga con una larghezza delle corsie di 4,05 metri e un’area con corsia stretta con tre corsie. Nella corsia larga tre carrelli retrattili del tipo Linde R14 si occupano di stoccare il materiale, nella corsia stretta i sette carrelli commissionatori ad alto livello di prelievo Linde V modulari eseguono, oltre ai compiti di picking, anche il rifornimento. Il magazzino è rifornito da tre diverse fonti: i contenitori per grandi volumi giungono tramite un collegamento a ponte direttamente dal magazzino di rifornimento centrale limitrofo alla superficie di picking. i contenitori per piccoli volumi vengono prelevati precedentemente in un magazzino automatico e separato per i pezzi piccoli e consegnati tramite il sistema di trasporto interno. i completamenti vengono approntati secondo le necessità nell’area di montaggio preliminare collegata alla superficie di picking.
Ergonomia e sicurezza svolgono un ruolo importante
Il picking nei magazzini verticali avviene esclusivamente con i carrelli commissionatori ad alto livello di prelievo Linde V modulari. Dal carrello elevatore i collaboratori prelevano il materiale necessario a un’altezza pari fino a 6,50 metri e con esso riforniscono i carrelli con rete metallica alti circa 1,80 metri e larghi circa 1,60
metri che contengono al massimo 500 chilogrammi di peso. Su un carrello vengono posizionati fino a tre ordini di picking. Affinché i collaboratori possano afferrare facilmente il materiale nel compartimento dello scaffale i carrelli commissionatori ad alto livello di prelievo dispongono di sbarre inclinate integrate. «Questa opzione di dotazione è un autentico elemento di differenziazione di Linde che possiamo utilizzare al meglio nei nostri nuovi magazzini verticali», sottolinea Jens Kernbach, responsabile della logistica del capannone presso Heidelberg. «Infatti, anche da Heidelberg siamo consapevoli del cambiamento demografico e responsabili nei confronti dei nostri collaboratori.»
Affinché il picking si svolga assolutamente senza difficoltà o attriti, gli apparecchi si muovono per induzione all’interno delle corsie tra gli scaffali. In tal modo l’operatore può concentrarsi completamente sulla procedura di picking e si muove alla distanza ottimale dallo scaffale. Rientra nell’ulteriore dotazione del carrello elevatore un assistente per sicurezza di corsia che frena l’apparecchio in caso di necessità in modo controllato fino all’arresto. «Possiamo quindi escludere danni allo scaffale o agli
apparecchi», racconta soddisfatto il responsabile di progetto Heger. Inoltre, gli ingressi del magazzino sono stati messi in sicurezza con barriere fotoelettriche. Esse fanno scattare immediatamente un allarme se persone non autorizzate entrano nell’area che è destinata soltanto ai carrelli elevatori. Inoltre, sugli apparecchi è pre-installato il sistema semiautomatico di navigazione in magazzino di Linde che offre potenziale per ulteriori ottimizzazioni. Infatti, con questa soluzione basata su RFID, i carrelli commissionatori ad alto livello di prelievo navigano nella corsia tra gli scaffali senza alcun intervento dell’operatore nella linea caratteristica ottimale fino alla postazione stabilita.
Grazie alla guida nella corsia tramite induzione possiamo escludere danni agli scaffali o ai carrelli commissionatori ad alto livello di prelievo.
Stefan Heger, responsabile di progetto
Flessibile e poco ingombrante con i trenini di movimentazione
Tre trenini di movimentazione in totale, chiamati da Linde Load Train, portano i carrelli caricati con la merce dalla stazione di consegna agli operai sulle linee di produzione. Sono costituiti da un trattore del tipo Linde P50, in funzione di motrice, e da uno o due carrelli con montanti ad arco con sterzo integrale e larghi listelli di sollevamento. Ogni rimorchio consente il trasporto contemporaneo di rispettivamente due carrelli che, grazie alla mancanza dell’asse centrale, possono essere inseriti su entrambi i lati o rimossi. «Ciò ci permette di pianificare i percorsi in modo flessibile», spiega il responsabile di progetto Stefan Heger. Un ulteriore vantaggio è l’ingombro inferiore del Load Train di Linde che si muove seguendo la traiettoria su una corsia larga 2,20 metri.
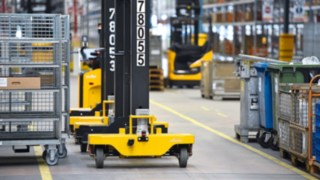
Bilancio positivo, ma l’ottimizzazione continua
Anche dopo la conclusione dell’investimento il responsabile della logistica di stabilimento Ehmler cerca ancora potenziale di ottimizzazione. Si aspetta di ricevere supporto, tra l’altro, dal modulo «analisi dell’utilizzo» della soluzione per la gestione flotta di Linde. Ehmler: «Utilizziamo 'connect:' già da molti anni per controllare l’accesso ai carrelli elevatori e rilevare gli urti e abbiamo raccolto esperienze molto positive con questo strumento. Adesso possiamo anche utilizzare il software per ottimizzare i nostri processi e, ad esempio, aumentare ulteriormente lo sfruttamento degli apparecchi.»
Ormai è trascorso quasi un anno dalla messa in pratica del nuovo progetto dell’intralogistica basato sul principio di magazzino verticale, carrelli commissionatori ad alto livello di prelievo e trenino di movimentazione presso Heidelberg. E le conclusioni tratte da Matthias Ehmler sono decisamente positive: «Abbiamo messo in pratica il progetto non soltanto rispettando tempi e costi previsti, ma anche raggiungendo il nostro obiettivo di una logistica snella. Siamo sicuramente una referenza positiva per Linde e Suffel.»
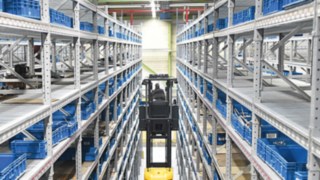