Wie zwei automatisierte Helfer für effiziente Warentransporte sorgen
Warenfluss statt Warteschleife
Wenn die Nachfrage – und damit das Produktionsvolumen – steigt, ist das eigentlich ein Grund zur Freude. Doch wie lässt sich der intensivierte Warenfluss bewältigen, ohne die Beschäftigten mit immer wiederkehrenden Transportaufgaben zu belasten? Beim Kunststoffverarbeiter Poloplast lautet die Antwort: Automation, made by Linde MH.
„Und nun zum Verkehr: Heute herrscht freie Fahrt, alles läuft flüssig, es ist mit keinen Behinderungen zu rechnen. Damit allen einen angenehmen Tag!“ Über solche Nachrichten freut man sich auf dem Weg zur Arbeit oder dem Weg in den Feierabend. Wenn es dann sogar noch während des eigentlichen Arbeitstages staufrei zugeht – umso besser. Was Letzteres anbetrifft, haben die Mitarbeitenden der Poloplast GmbH & Co. KG im oberösterreichischen Leonding das Glück auf ihrer Seite – oder anders formuliert: zwei automatisierte Linde-Hochhubwagen vom Typ L-MATIC.
Ein Blick zurück: Warentürme in der Produktion
Bei Poloplast, einem der Branchenführer in der europäischen Rohrindustrie, hatte das ständig wachsende Produktionsvolumen über die Jahre zu einem handfesten Stau-Problem in einer bestimmten Produktsparte geführt. Denn neben grossen Rohren für Kanalsysteme und Co. stellt das Unternehmen auch kleinere Artikel für den Hausabflussbereich her. Diese werden in Kartons gepackt und dann teils manuell, teils automatisch auf Europaletten geladen. Die Aufgabe, fertige Paletten von der Produktion ins Lager zu verbringen, fiel jeweils den Kolleginnen und Kollegen der Frühschicht zu, die den Transport von Montag bis Freitag per Routenzug erledigten. „Wir arbeiten hier sieben Tage im Vierschichtsystem. Wenn die Leute dann morgens ihren Dienst antraten, hatte sich über die Nacht einiges angesammelt – ganz zu schweigen von Montagfrüh. Dann türmte sich quasi der gesamte Wochenend-Output in der Produktion“, erklärt Poloplast-Logistikleiter Ralph Wagenhuber.
Da lag es quasi auf der Hand, über Automation nachzudenken.
Die Poloplast-Verantwortlichen gingen bereits mit relativ konkreten Vorstellungen in den Anbieter-Check. Wagenhuber: „Uns kam es zum einen natürlich auf grösstmögliche Zuverlässigkeit an; zugleich wollten wir aber auch eine Lösung, die ohne grosse Änderungen an unserer bestehenden Infrastruktur auskommt – also eben ohne Spiegel, Führungsschienen und so weiter –, sodass wir im Bedarfsfall Fahrwege problemlos anpassen können.“
Darüber hinaus stand der Sicherheitsaspekt ganz oben im Lastenheft, schliesslich herrscht zwischen Produktion und Lager stets reger Stapler- und Fussgängerverkehr. „Dieser ‚Wunschzettel‘ führte uns relativ schnell zu Linde MH, die in unserer Stapler- und Flurförderzeugflotte ohnehin schon ziemlich breit vertreten sind“, erläutert Logistikleiter Wagenhuber.
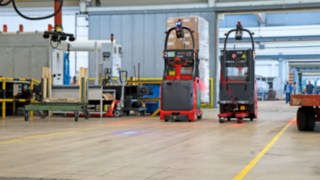
Die autonomen Fahrzeuge haben die „Karte im Kopf“ …
Gemeinsam mit den Warenumschlagsprofis aus Aschaffenburg implementierte man bei Poloplast im Projektverlauf zwei autonome Hochhubwagen Linde L-MATIC. Die liebevoll „Tom“ und „Jerry“ getauften Fahrzeuge verkehren dank Geo-Navigation völlig selbstständig (und natürlich friedlich) zwischen dem Durchlauflager sowie den insgesamt neun Aufnahmeplätzen. Acht davon werden manuell bedient; das heisst, die Beschäftigten bepacken Paletten mit Kartons und rufen nach Fertigstellung die Linde-Geräte per Knopfdruck.
Darüber hinaus existiert ein automatischer Wickelautomat, der eigenständig von den Hochhubwagen angefahren und von den fertig verpackten, folierten Paletten „befreit“ wird.
… und sind perfekt in die Prozesse integriert
Auf ihrem Weg ins Lager passieren Tom und Jerry Rolltore, die über Comboxen mit den Fahrzeugen kommunizieren und sich dadurch selbsttätig öffnen und schliessen. Im Durchlauflager mit Gefällerollbahnen angekommen, erkennen die Linde L-MATIC ausserdem, welche der sieben Bahnen gerade frei ist. Wagenhuber: „Dafür haben wir pro Regalfach eine Lichtschranke installiert. Wenn ein Fach gefüllt ist, erhält das Linde-Gerät über die Combox eine entsprechende Information und fährt zum nächsten freien Platz.“
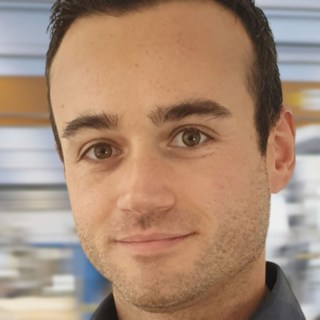
Offengestanden könnten wir uns die Abläufe hier kaum noch ohne die beiden Linde L-MATIC vorstellen.
Ralph Wagenhuber, Logistikleiter bei Poloplast
Modernste Systeme sorgen für Sicherheit
Selbständig be- und entladen – und: selbstständig laden. Auch das gehört zum Leistungsportfolio von Tom und Jerry. „Wenn gerade kein Auftrag da ist, fahren die Geräte bei etwa 40 Prozent Akkuenergie zur Ladestation und holen sich für circa 15 Minuten Power-Nachschub. Mit diesen kleinen Zwischenladestopps stellen wir sicher, dass die beiden praktisch 24/7 unterwegs sein können“, zeigt sich Wagenhuber zufrieden. Zufrieden ist man in Leonding übrigens auch mit dem umfassenden Sicherheitskonzept aus dem Hause Linde MH: So machen Tom und Jerry nicht nur per Linde BlueSpot™ auf sich aufmerksam; zusätzlich projizieren die Fahrzeuge per LED seitlich sowie in Fahrtrichtung gut sichtbare rote Streifen auf den Hallenboden. Und natürlich stoppen die Geräte automatisch, sobald sich ein Mensch zu nahe im Frontbereich bewegt.
Output: gesteigert – Warenfluss: sichergestellt
Sieht man Tom und Jerry bei der Arbeit zu, wie sie – ganz im Gegensatz zu ihren berühmten Zeichentrick-Namensvettern – in aller Gelassenheit ihre Bahnen ziehen, könnte man fast vergessen, dass die Geräte alles andere als eine ruhige Kugel schieben. Circa 60.000 Paletten werden von dem leistungsstarken Duo Jahr für Jahr aufgeladen, transportiert und abgeladen. „Offengestanden könnten wir uns die Abläufe hier kaum noch ohne die beiden vorstellen. Die Leute in der Frühschicht müssen sich nicht mehr mit den langen Streckentransporten abmühen, wir haben Platz für neue Maschinen gewonnen und konnten durch den kontinuierlichen Warenfluss unseren Output signifikant steigern“, bilanziert Wagenhuber. „Dem Stau weint hier niemand eine Träne nach.“
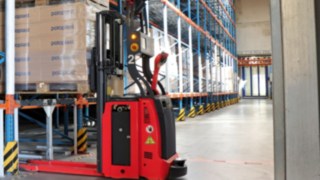
Poloplast GmbH & Co. KG
Die Poloplast GmbH & Co. KG ist ein Kunststoffverarbeiter mit Sitz im oberösterreichischen Leonding nahe Linz und zählt zu den Branchenführern der europäischen Rohrindustrie. Das international tätige Unternehmen entwickelt, produziert und vertreibt vorwiegend verstärkte, mehrschichtige Rohrsysteme aus Kunststoff – für den Hausabflussbereich, aber ebenso für den Kanalbau. Gemeinsam mit seinen Tochterunternehmen beschäftigt Poloplast aktuell rund 370 Mitarbeiterinnen und Mitarbeiter. In Sachen Intralogistik vertraut der Kunststoffspezialist überwiegend auf Fahrzeuge aus dem Hause Linde Material Handling; neben den beiden autonomen L-MATIC-Fahrzeugen sind in Leonding auch Elektro- und Diesel-Gegengewichtsstapler im Einsatz.