BASF Italia
Optimierung ist eine Frage der Chemie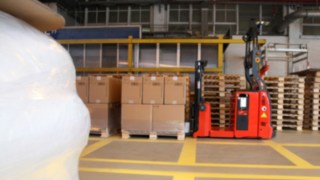
Einfach heisst nicht immer banal: Beweis hierfür ist das Automatisierungsprojekt von Linde Material Handling für BASF Italia. Zur Optimierung der Effizienz und Sicherheit wurde auf Grundlage des automatisierten Fahrzeugs eine flexible, sichere und schnell umsetzbare Lösung für die Logistik 4.0 integriert.
Qualität auf Molekularebene
BASF ist ein Chemieunternehmen mit 110.000 Mitarbeitern weltweit, das fast alle Industriesektoren und Länder mit Produkten beliefert. Im Werk von Pontecchio Marconi in Italien, werden Zusatzstoffe für Kunststoffe und insbesondere Lichtstabilisatoren und Antioxidationsmittel hergestellt.
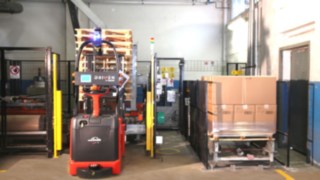
Automatisierter Stapler von Linde im Einsatz bei BASF
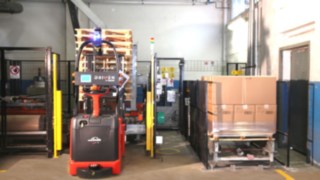
Automatisierter Stapler von Linde im Einsatz bei BASF
Das Werk in der Provinz von Bologna, das nach hohen Sicherheitsrichtlinien (Seveso III-Richtlinie) arbeitet, übernimmt eine wichtige Rolle innerhalb des Logistik- und Produktionsnetzwerks von BASF. Das Unternehmen ist direkter Lieferant für Kunden und Lager in mehr als 50 Nationen weltweit.
Vom Problem zur Lösung
Wir haben uns an Linde gewandt, um eine einfache, aber effiziente und massgeschneiderte Lösung zu finden.
Mario Serranti, Supply Chain and Logistic Manager von BASF
Standardisierung und Anpassung bestens kombiniert
Linde schaffte für BASF Italia eine automatisierte Lösung, welche das strenge Protokoll, um maximale Sicherheit für jeden Tätigkeitsbereich zu gewährleisten, einhält. Eine erste Arbeitsplatzsicherheitsanalyse war deshalb wesentlicher Bestandteil des Projekts. „Als die von Linde entwickelte Lösung Form annahm, haben wir sofort das Potenzial aus Sicht der Automatisierung und vor allem aus Sicht der Sicherheit erkannt“, so Mario Serranti.
Die von Linde entlang der Lieferkette von BASF integrierte Lösung mit FTS ermöglicht die Automatisierung einer Tätigkeit mit geringem Mehrwert und optimiert die Sicherheit. Das FTS-System arbeitet selbständig auf beschränktem Raum ohne Interaktion mit dem Mitarbeiter. Diese innovative Lösung unterstützt BASF auf dem Weg in Richtung Industrie 4.0.
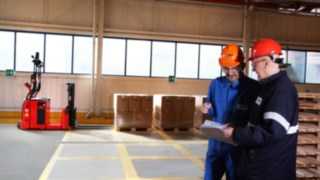
Konfigurierbar bis ins kleinste Detail
„Die Stärke der von Linde implementierten Lösung liegt in ihrer maximalen Konfigurierbarkeit. Standardfahrzeuge werden durch eine direkt in die IT-Infrastruktur des Kunden geladenen Überwachungssoftware zu „intelligenten“ Fahrzeugen. Der Stapler kommuniziert direkt mit der Verpackungsanlage: Somit gibt die Anlage die Zeiten vor und fordert das Fahrzeug zur richtigen Zeit auf, eine fertige Palette zu entnehmen oder den Prozess mit einer leeren Palette zu versorgen“, berichtet Serranti.
Für die Installation waren keine Änderungen an der Infrastruktur nötig, sondern nur die Installation eines Lasers am Fahrzeug. Dieser misst den Abstand zu den wichtigsten Infrastrukturen im Lager und vergleicht diese mit der in der Software geladenen Karte des Arbeitsbereichs. Auf diese Weise kann sich das automatisierte System von Linde in einem realen Raum, der im Speicher des Staplers virtuell reproduziert wird, bewegen. Dank der genauen Analyse im Vorfeld vergingen von der Planung bis zum Regelbetrieb nur wenige Monate.
Alle Elemente für die Sicherheit
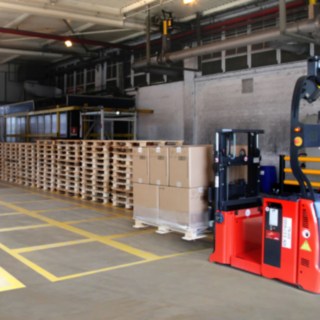
Vor allem die Gewährleistung der Sicherheit und die Verbesserungen dieser lagen bei diesem Projekt im Vordergrund. Das Projekt umfasst alle Sicherheitseinrichtungen, die von der Richtlinie für automatisch geführte Maschinen vorgeschrieben sind. Nach einer Risikobeurteilung wurden mit dem Kunden alle Vorschriften des Betriebs mit in das Angebot von Linde Robotics eingearbeitet.
Im Einzelnen ist der Stapler mit mehreren Lasern ausgestattet, welche die Umgebung in alle Richtungen kontrollieren. Ein Laser überwacht die Tätigkeit der Gabeln und die Ladung auf diesen. Ein parallel zur Bodenebene verlaufender Laser erfasst Hindernisse, bei denen das Fahrzeug automatisch abbremst. Darüber hinaus ist der Stapler mit einem doppelten Not-Aus-Knopf, einer akustischen Warnvorrichtung und dem BlueSpot™ ausgestattet. Durch dieses Sicherheitspaket wird eine maximale Sicherheit des FTS-Systems gewährleistet.
Ein flexibles Projekt
"Das integrierte Projekt ermöglicht es uns, sofort auf Veränderungen zu reagieren. Vor allem die Skalierbarkeit ist ein grosser Vorteil. In einem globalen Markt, der sich kontinuierlich und schnell wandelt, ist eine Prognose zur Entwicklung der mittelfristigen logistischen und produktiven Ströme schwierig.“ erklärt Mario Serranti. Bei BASF arbeiten die automatisierten Stapler heute in zwei Tagesschichten. Die Geschwindigkeit kann dabei mit dem Anstieg des Auftragsvolumens erhöht werden oder die Fläche der vorübergehenden Lagerung erweitert werden. Die Arbeitsgänge können jederzeit neu konfiguriert werden.
Die Sicherheit ist für BASF der wichtigste Vorteil von allen: Heute arbeitet das FTS-System ohne Risiko von Störungen mit dem Bedienungspersonal und der Stapler wird automatisch und ohne jeglichen Kontakt angehalten, wenn sich ein Bediener nähert.
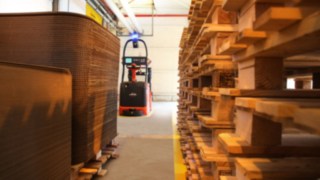
Automatisierter Stapler von Linde bewegt Holzpaletten
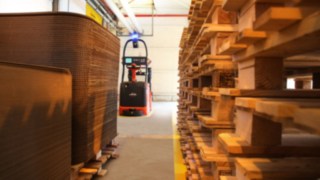
Automatisierter Stapler von Linde bewegt Holzpaletten
Die Umsetzung ist ein perfektes Beispiel für die Optimierung, die ein Projekt der Industrie 4.0 in ein Unternehmen einbringen kann: ein hohes Mass an Innovation in einem einfachen, aber nicht banalen System, das es ermöglicht, die Arbeit der Belegschaft aufzuwerten und ein sicheres Arbeiten zu gewährleisten. Das FTS-System hat zu einer Verbesserung der Abläufe bei der Verpackung geführt – zum Vorteil des gesamten Betriebs. Und so wurde die Chemie der Optimierung in die Wege geleitet.
Flexibilität ist ein entscheidender Wert, in den man investieren muss.
Mario Serrant, Supply Chain and Logistic Manager von BASF
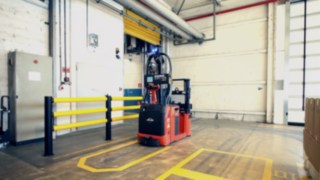